不少生产制造企业对于能源消耗都很头疼,水泥生产厂就位列其中。根据《2009水泥厂运营手册》,使用干法窑平均每生产1吨水泥就要消耗100-200千瓦时的能源,所以水泥厂在能源成本上面临着成本上升的巨大压力。这种复杂的竞争,加上日益升高的燃料和能源成本,促使水泥生产厂商使用能源管理程序,以帮助其降低成本,维持竞争力和盈利水平。
全面的工业能源管理能够帮助生产厂商和流程型制造企业降低能耗。很多水泥生产厂商在采用了全面的能源管理以后,能源成本降低了20%。一个具有战略性的方案能够帮助用户识别哪些措施可以降低成本,以及哪些工具能够降低成本,例如:
■ 电力及能源管理系统;
■ 变频器;
■ 模型预测控制系统;
■ 能源评估。
能够帮助水泥生产企业的工具如下:
■ 发现并消除低效率环节;
■ 修正设备和流程;
■ 产品设计中提升能效;
■ 扩展工厂的运作模式以引入全面的能源管理程序,实现可量化的节能和成本降低。
在管理生产的同时,平衡供应、定价、需求、过程效率、法规依从和其他要求之间的关系是很困难的。同时,能源成本的升高使这些竞争进一步加剧,包括水、空气、汽油、电能和蒸汽。
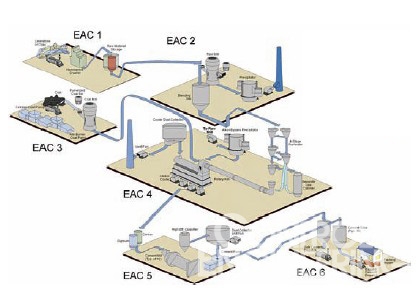
将工厂划分为多个能源分布中心(EAC)。资料来源:Rockwell Automation公司。
美国能源部工业技术项目(Industrial Technologies Program)的技术经理Paul Scheihing说道:“购买工厂生产所需要的能源被看做管理输入,通常都会备受关注,但是一旦这些能源被采购进入工厂,那么它们的使用仅仅被看做成单纯的运营成本。对于所有工业工厂来说,这都是不现实的。经验表明,如果一家工厂并未主动进行能源用度管理并且没有备案明确的能源用度计划,那么这家工厂的效率将是极低的。如果没有相应的性能指标将能耗与产量联系起来,就很难量化或者明确能源强度到底是否有所改善。”
工业界开始在自动控制、最优化和信息解决方案方面敢于直面能源的挑战,并乐于接受可以量化的结果。
能源评估
在开始能源管理程序之前,首先进行一次能源评估,可以帮助企业找到着手点,以降低能源消耗。能源评估可以很简单,例如在建筑物或者工厂中走一遍,就能发现很多显而易见的着手点,或者发现更加具体的努力方向。评估能够帮助建立节能的范畴、定义关键指标并使资源到位,以纵览整个企业的能源用度情况。
评估的建议可能包括行为方式的改进,例如将维护作业安排在非峰值生产时间,或者更复杂的,例如将更改写入设备的程序中。在分析中还可以包括资本改善的评价和优化。
能源监控
在评估之后,管理能源消耗的第一步就是明确整个工厂的能源使用模式和趋势。
大楼管理人员能利用工厂设施的计量设备,包括电力监控设备和历史公共能源账单,在进行能源或者过程评估之前,首先搜集设备的能源用度和环境条件数据。这个过程应该包含所有使用能源的地点,从工业过程到关键建筑物系统。
这些数据随后被能源历史软件录入并加上时间标记,以建立能源品质和能源消耗的趋势分析和比较,以及未来改进的基准。有了这张厂区能源用度的总图,大楼管理人员就能够发现问题所在,选择做一些改变以减少能源消耗和相应的成本,例如将负荷降低或者在工厂快要接近峰值使用时暂时降低供电电压。
能源计量
第一步是计量主要的公用能源流入,并将厂区划分成多个能源分布中心(Energy allocation centers, 简称EAC)。在控制电能消耗方面,厂家可以在发电机、工厂变电站、窑、超过200马力的电机和每个EAC内的主要用电设备处安装总电表。
对于化石燃料消耗的控制,厂家可以计量主要燃气表和窑的流入量,和主要的天然气消耗大户的用量。生产设备监控也提供了设备的能源消耗信息。在设备和流程中找到有用的数据搜集点,对信息系统进行编程,存储并分析这些数据。
负载分析可以将能源用度量绘制成图,通过测量并记录能源用量来找到能源需求峰值区间,将工厂运行和产量与能源消耗实时地联系起来,预测能源需求。
电能质量监控:搜集并审查电源质量信息能够帮助识别电能系统的异常状态,计算诸如断电成本之类的数据。
电能质量监控可以完成测量、显示、记录、趋势分析等任务,并根据电能质量参数进行预警,例如谐波、电压偏移和配电系统事件。
有了历史数据,大楼管理人员就能够发现电能质量问题,例如电压暂降或者谐波,这些问题会对工厂中的设备造成损坏,并给电网带来功率因数问题。知道了这些风险,制造厂商就可以更好地保护他们的设备,避免电力公司的罚款。
“如果一家工厂并未计划并且主动进行能源用度管理,那么这家工厂的效率将是极低的。”
提高效率:接下来,水泥生产厂商可以采用控制策略,例如紧急减负荷、成本分配和需求管理,帮助提升整个工厂的能源效率。
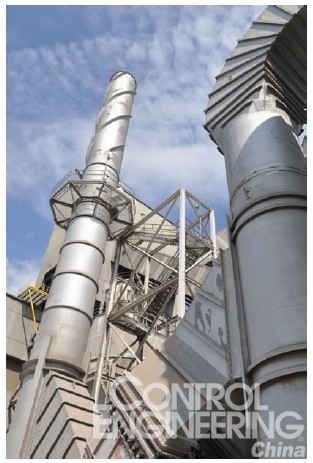
水泥生产企业可以改进控制策略,例如紧急减负荷、用量分配和需求管理,以帮助提升整个工厂的能源效率。资料来源:Rockwell Automation
紧急减负荷:如果质疑紧急减负荷系统的成本是否合算,只需要将早期进行的评估过程收集到的数据分析一下,就知道一旦供电中断会带来多少生产损失。大多数水泥生产厂商发现紧急减负荷方案还是利大于弊的,它的成本也就相当于一两次电力中断所带来的损失费用。
紧急减负荷可以应用于具有发电机或者多个公用电网源的现场,帮助生产厂商保护发电机远离危险、过载,在断电期间维持关键负载,优化电源和关键负载,减少由设备损坏和停机带来的成本。
能源消耗、成本分摊、隐性计费:浏览之前搜集的能源用度数据,水泥生产厂商能够发现能源是在什么地方以什么比例被消耗掉的,进而在部门、过程或者工厂之间分摊成本;通过“隐性计费”来核对公用能源账单;评估替代能源的效率和合同。

生产设备监控能够提供特定设备的能源消耗信息。资料来源:Rockwell Automation公司。
需求管理系统通过减少负荷并使用调峰策略来限制能源需求,帮助减少需求费用并管理实时能源采购,或者在紧缩时期使负载最小化。
例如,炼钢厂每个月要使用90,000兆瓦时的电能,每年的电费是270万美元。通过将不可靠的需求管理系统更换掉,并更新其控制算法,以更有效地减少负荷、提升功率因数并减少电压暂降,这套价值30万美元的系统在5个月内就能收回成本。由于将损耗降低,它每个月还能带来7万美元的节约。
电机管理
工厂中大约70%的电力都是被各种电机驱动系统消耗掉的。在10年的生命周期中,一台电机所消耗的能源成本是电机本身价格的100倍。
水泥制造厂通过安装智能电机控制解决方案可以极大地降低电机能源消耗,例如变频器。在水泥制造厂中,变频器能够节省能源,控制过程参数和变扭矩特性的保留时间,例如气流和液体流,恒扭矩应用中也同样适用,例如物料夹持和碾压设备。驱动器也被用来为滚筒碾压机供电,将矿渣压制成水泥,也可以用来启动和运行多种滚筒碾压机、球磨机和传送带。
水泥厂中典型的变频器应用包括:抽/送风扇、窑驱动、磨驱动、物料夹持系统、离心泵和风扇以及压缩机的控制。
功率因数(PF)能够测量水泥制造厂从电网获得的电能的使用状况。PF为1代表100%的效率,即所电能被完全使用。PF为0代表所有的功率均为无功功率。为了提高功率因数,必须采用变频器,使用同步电机(此类电机的功率因数为1),或者安装功率因数校正电容。功率因数校正电容能够改善感应电机的较差的功率因数。
优化效率:既然水泥制造厂已经发现了提升效率的机会,那么下一步就是审视这些机会,优化所有过程。事实上,有效地控制一个主要的过程单元通常意味着使用多变量系统。在大多数情况下,独立处理每个控制循环以获得最优控制并不适用于多变量系统,因为每一个循环的控制动作都会互相影响。
模型预测控制(Model predictive control, 简称MPC)提供了过程的内部动态模型,它依从于过程约束条件,并且给予固定的频率周期;历史控制动作可以用来对比偏差;横向对比得到的最优化成本方程可以用于计算最优化控制动作以及未来控制行为。
MPC技术允许控制器接受当前过程工作状态的信息,然后使用模型预测过程对一系列未来动作在特定输入下和特定时间内或者所谓的“预测视野”内作出响应。下一步,最优控制问题可以在线解决,它决定了在多个操作变量下未来动作的最佳顺序,以便在遵守各种过程约束条件下,尽量减少特定目标函数。将控制轨迹应用到过程上,新的过程测量值就可以反应修正后的运行状态,将过程输出与预期的控制轨迹对比。有了这些新的信息,系统就可以重复最优状态和最优控制动作。
MPC系统能够最优化原材料制备过程,包括预处理、水泥研磨和原材料混合。通过最优化燃烧、温度控制、热恢复过程等步骤,可以极大地节约能源。MPC系统将能源消耗削减3%到5%,并能提供更高的产品质量和设备能力的提升。