AI温度控制器与传感器的配合应用
关键词: 输入信号、传感器
一、测量控制系统的组成
在自动控制回路中主要由输入传感器、调节仪、输出执行装置与被控对象四个部分组成,其系统结构图如图所示。
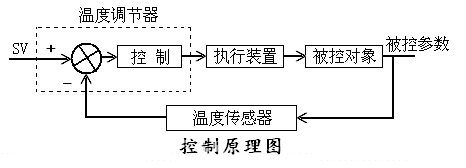
现代传感器在原理与结构上千差万别,如何根据具体的测量目的、测量对象以及测量?环境合理地选用传感器,是在进行某个量的测量时首先要解决的问题。当传感器确定之后,与之相配套的测量调节和被控设备也就可以确定了。测量控制结果的成败,在很大程度上取决于传感器的选用是否合理。
在仪表的使用过程中要充分了解输入传感器技术规格特性,才能更好的应用仪表。选择合理的输入模块才能更好的应用仪表。如:I4模块应用在二线制变送器,同时馈电24VDC;如:I2模块应用在频率输入,馈电12VDC;J0模块热电阻;J1模块热电偶等。
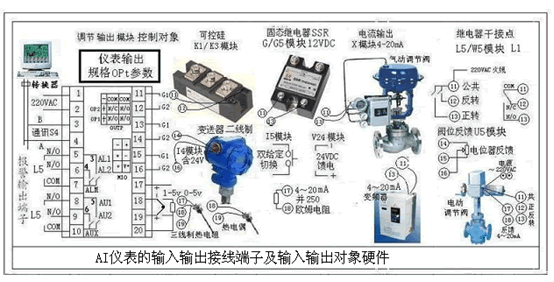
二、仪表常用输入规格
以AI-808仪表为例一台仪表可以兼容常规所有输入规格入下:
热电偶:K、S、R、E、J、T、B、N 热电阻:Cu50、Pt100
线性电压:0-5V、1-5V、0-1V、0-100mV、0-20mV等
线性电流(需外接分流电阻):0-10mA、0-20mA、4-20mA等
扩充规格:在保留上述输入规格基础上,允许用户指定一种额外输入规格(按特殊分度表输入)
●测量范围:
热电偶:K(-50-+1300℃)、S(-50-+1700℃)、R(-50-+1650℃)、T(-200-+350℃)
E(0-800℃)、J(0-1000℃)、B(0-1800℃)、N(0-1300℃)
热电阻:Cu50(-50-+150℃) 、Pt100(-200-+600℃)
线性输入:-1999-+9999由用户定义
●测量精度:0.2级(热电阻、线性电压、线性电流及热电偶输入且采用铜电阻补偿或冰点补偿冷端时) 0.2%FS±2.0℃(热电偶输入且采用仪表内部元件测温补偿冷端时)
●响应时间:≤0.5秒(设置数字滤波参数dL=0时)
注:仪表对B分度号热电偶在0-600℃范围时可进行测量,但测量精度无法达到0.2级,在600-1800℃范围可保证0.2级测量精度。
在确定传感器型号后在仪表参数表设定传感器代号就能正常显示测量数据。表格如下:
代号 传感器输入类型 代号 传感器输入类型
0 K 20 Cu50
1 S 21 Pt100
2 R 22 0~75mV电压输入
3 T 26 0~80欧电阻输入
4 E 27 0~400欧电阻输入
5 J 28 0~20mV电压输入
6 B 29 0~100mV电压输入
7 N 30 0~60mV电压输入
8 WRe3-WRe25 31 0~1V
9 WRe5-WRe26 32 0.2~1V
10 客户自定义 33 1~5V电压输入
12 F2辐射高温温度计 34 0~5V电压输入
Sn=10时,采用外部分度号扩展,用户可以自输入非线性输入表格。
三、输入信号类型:
第一类、温度传感器
1、热电偶与热电阻一样都是温度传感器,但是他和热电阻的区别主要在于:
1.1 信号的性质,热电阻本身是电阻,温度的变化,使电阻产生正的或者是负的阻值变化;而热偶,是产生感应电压的变化,他随温度的改变而改变。
1.2 两种传感器检测的温度范围不一样,热电阻一般检测-200~800度温度范围;热偶可检测0-2300度的温度范围(甚至更高)所以,前者是低温检测,后者是高温检测。热电阻是阻值随温度的变化而变化,而热电偶输出是毫伏信号。热电阻测量范围0到几百摄氏度,精度要比电偶的高,电偶测温范围可达一千多度。电偶测温反应时间要比电阻的快。
1.3 从材料上分,热阻是一种金属材料,具有温度敏感变化的金属材料,热偶是双金属材料,既两种不同的金属,由于温度的变化,在两个不同金属丝的两端产生电势差。
2、热电偶的基本构造及如何选型:
2.1测温热电偶是利用两种金属之间的热电现象来测温的。在两种不同金属导体焊成的闭合回路中,若两焊接端的温度不同时,就会产生热电势。这种由两种金属导体组成的回路就称为热电偶。实用的热电偶只焊接一端,此焊接的一端称为热端(工作端),另一端不焊接而是接入测量仪表,称为冷端(自由端)。当热电偶冷端和热端的温度不同时,就会产生热电势,其值与组成热电偶的材料性质、冷端和热端的温差大小有关、而与热电极的长度、直径无关。
2.2测量精度和温度测量范围的选择。使用温度在1300~1800℃,要求精度又比较高时,一般选用B型热电偶;要求精度不高,气氛又允许可用钨铼热电偶,高于1800℃一般选用钨铼热电偶;使用温度在1000~1300℃要求精度又比较高可用S型热电偶和N型热电偶;在1000℃以下一般用K型热电偶和N型热电偶,低于400℃一般用E型热电偶;250℃下以及负温测量一般用T型电偶,在低温时T型热电偶稳定而且精度高。
2.3仪表对B分度号热电偶在0-600℃范围时可进行测量,但测量精度无法达到0.2级,在600-1800℃范围可保证0.2级测量精度。
2.4热电阻与热电偶的特殊用途:用2支PT100铂电阻可用于干湿球温湿度测量;温差测量将2支热电偶反并联测量温度差,应用在空调系统的进出水温差测量。
3、热电阻的基本构造及如何选型
铂热电阻是利用铂丝的电阻值随着温度的变化而变化这一基本原理设计和制作的,按0℃时的电阻R℃100欧姆(分度号为PT100)等,PT100测温范围均为-200~800℃。感温元件骨架的材质也是决定铂热电阻PT100使用温区的主要因素,常见的感温元件有陶瓷元件,玻璃元件,云母元件,它们是由铂丝分别绕在陶瓷骨架,玻璃骨架,云母骨架上再经过复杂的工艺加工而成。由于骨架材料本身的性能不同,陶瓷元件适用于850℃以下温区,玻璃元件适用于550℃以下温区。近年来市场上出现了大量的厚膜和薄膜铂热电阻PT100 感温元件,厚膜铂热电阻PT100元件是用铂浆料印刷在玻璃或陶瓷底板上,薄膜铂热电阻PT100元件是用铂浆料溅射在玻璃或陶瓷底板上,再经光刻加工而成,这种感温元件仅适用于-70~500℃温区。
第二类、二线制变送器及线性电流输入信号
1.应用类型
将物理测量信号或普通电信号转换为标准的电信号输出一般分0~20mA、4~20mA、0~5V、1~5V等作为:温度/湿度变送器,压力变送器,差压变送器,液位变送器,电流变送器,电量变送器,流量变送器,重量变送器、红外温度变送器等信号的输出。
模块选择:电流模块I4;
2.变送器量程范围的确定
测量物理量的变送器量程范围的选择要求是大于常用量程的1/3为好,特别是压力测量,因为压力波动大,会造成超量程损坏变送器,影响正常仪表显示。
3.信号范围定义及量程扩展
二线制变送器的信号是大家已经很熟悉的DC 4-20mA直流电流信号。该DC 4-20mA直流电流信号抗噪讯能力很强,即使在有电力设备的环境下都可以保证信号的稳定传送。
信号回路上是4-20mA的电流信号。二线制变送器利用输入信号0%对应4mA的直流电流动作。信号为100%时,变送器就在4mA上加上16mA将回路的信号控制在20mA。在实际应用中传感器输入信号和4-20mA的输出信号成正比。
对应线性输入信号还需输入信号量程,有下限刻度值DIL与上限刻度值DIH来定义,所需显示的刻度数据。
量程扩展:有的线性输入信号是特殊的量程范围如电阻变阻器0~75mV的信号,可采用0~100mV输入规格,刻度量程按等分扩展就可以了。
第三类、电量/功率测量
近年来电量仪表数字化的迅速发展,可以将具备有互感器隔离的交流电压及交流电流信号输入,给数字显示仪表,实现数字显示、报警、变送、通讯功能。实现了普及应用,是指针式仪表的更新换代产品。
模块选择:电流I7、电压I8模块;
具备有互感器隔离的交流电压及交流电流信号输入的信号接入专用I7、I8模块就可测量电流、电压。
同时输入电流/电压就实现计算功率测量仪,具有2个上限报警2个下限报警、变送、通讯功能。
对于电度量的测量采用AI-601型高性能电流/电压/功率测量仪配合流量结算仪就可以按小数来累积电度量。
如:假定电流互感器为200:5,输入电压满刻度500VAC,因此功率满刻度为100KW,变送功率电流上限刻度为100定义,变送的电流给流量结算仪来计算电度,流量量程范围按100度/小数流量来计算电度数。
第四类、流量信号输入
以AI流量积算仪为例:可对物质的质量、体积、长度进行累积计算,并可进行批量控制。
流量输入信号可为1-5V、0-5V、4-20mA及频率等,温度信号可编程输入为Pt100热电阻、K、E、J型热电偶、电压或电流信号,压力信号可为各种电压或电流信号。
输入模块选择:电流I4(供电24V)、频率I2(供电12V);
AI-808H流量积算仪具备完整的温压补偿功能,无需更换不同的仪表或型号,通过编程即可实现一般气体、饱和蒸汽、过热蒸汽及液体的温压补偿运算。采用查表方式对蒸汽进行补偿运算,具有较高的精度。并可依照用户要求扩充补偿公式实现特殊功能,如对热量或其他物理量的累积,含水分天然气累积等。
流量温压补偿类型:
饱和蒸汽,压力补偿:参数选择bC =3;过热蒸汽,温度压力补偿:参数选择bC =4;
批量控制:
作为批量控制器使用时,具有独立的4位控制累积器及12位总累积器,及专门的显示模式,功能强大,操作方便。
作为批量控制器用(参数Act=1-255时)。做为批量控<

提交
AIMINI-DCS超小型监控系统在真空热处理炉应用
AIMINI-DCS超小型集散温湿度监控系统在文物保护的应用
AI温度调节无纸记录仪
自动干燥控温设备应用AI调节仪表
钟罩式烧结炉应用AI计算机监控系统案例